Calling Swift Solutions in Crisis
Facing a surge demand for healthcare during the COVID-19 pandemic, a leading ventilator company needs a swift solution to restore trust when quality complaints threatened their reputation, they turned to our team for help. Discover how we solve problems and support reliable service for global health.
Under covid-19, delivery time and quality are the keys to saving lives
In 2020, the world was struck by the COVID-19 pandemic, pushing healthcare systems to the brink of collapse. Intensive care units urgently needed life-supporting equipment like ventilators. As confirmed cases surged, orders for ventilators skyrocketed. Existing manufacturers struggled to meet this urgent demand due to capacity limitations and quality control issues.
Our client, an internationally leading ventilator company, decided to rise to the challenge, leveraging years of accumulated technology and experience to demonstrate their ability to scale production in an emergency.
At this critical moment, the company not only needed to rapidly increase production capacity but also had to ensure that every ventilator operated reliably and safely to support the lives of critically ill patients. However, frequent quality complaints and market pressure created a significant trust crisis, necessitating effective solutions to turn the situation around.
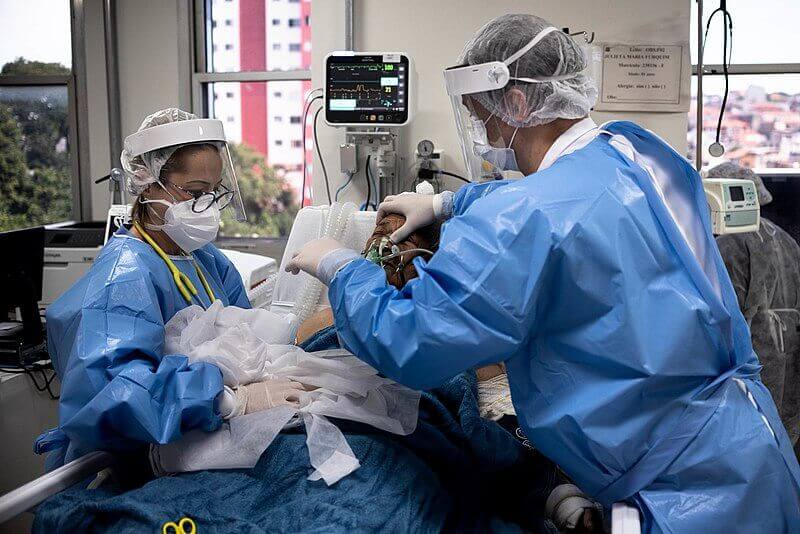
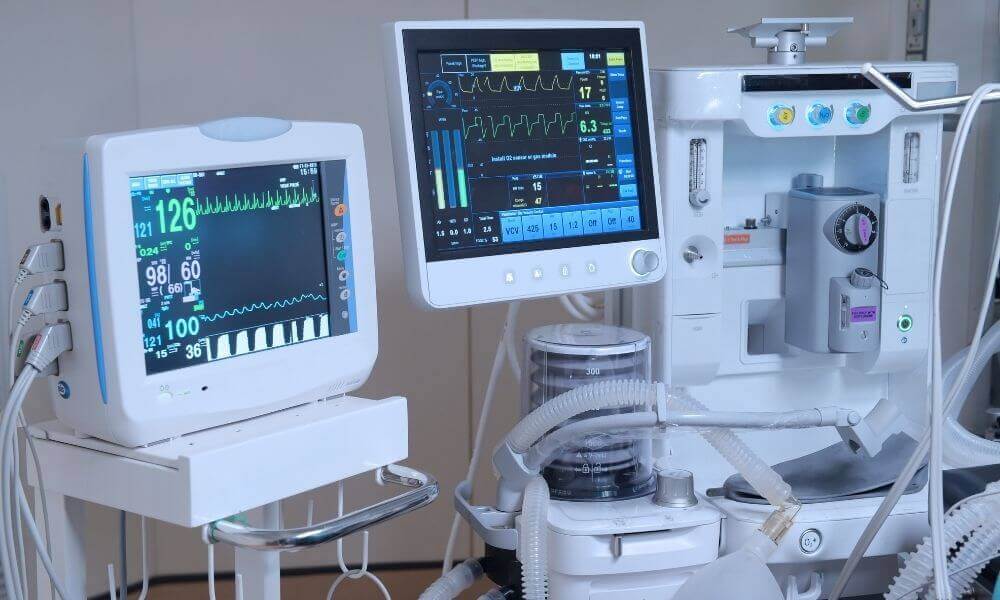
Stuck in a quality dilemma
Our client faced frequent quality complaints and were unable to meet the urgent need for effective patient treatment. The medical industry has strict requirements for the performance and reliability of ventilators; even minor defects could affect patient survival. Therefore, they urgently needed a practical solution to enhance product quality and restore customer confidence.
Optimizing the Production Reliability
Confronted with such a formidable challenge, our team quickly initiated in-depth technical analysis and design optimization.
First, utilizing Design for Manufacturing (DFM) software, we conducted a comprehensive evaluation of their product layout, optimizing pad packaging and component placement to ensure efficient and consistent production processes. This involved close collaboration with engineers to thoroughly understand product characteristics and the production environment, minimizing design-related defects.
Next, after identifying the issues, we performed a detailed process failure mode analysis, particularly focusing on the solder joint issues on the QFP (Quad Flat Package) PCB pads. By optimizing pad design and adjusting solder materials and process parameters, we significantly improved soldering quality, thereby reducing failure rates. This improvement not only enhanced production efficiency but also ensured that each ventilator’s reliability reached new heights.
Through these scientifically effective measures, we ensured that they could swiftly pivot their production line to meet the surging demand, contributing significantly to global efforts against the pandemic.
Delivered 5,000 ventilators with zero complaints
Finally we successfully achieved mass production of 5,000 sets of ventilators in just two weeks, with zero customer complaints. This high-quality delivery not only earned them customer trust but also made a vital contribution to the global fight against COVID-19 at a crucial time.